Indium Wire, made from high-purity indium metal, is prized for its exceptional malleability and thermal conductivity. Its low melting point and high ductility make it a preferred choice for soldering applications, particularly in electronics and semiconductor industries, ensuring dependable connections. With its compatibility across various materials and low reactivity, Indium Wire is ideal for bonding delicate components, finding applications in research laboratories, medical devices, and aerospace technology.
Indium wire is particularly advantageous for cryogenic sealing applications due to two key reasons: its ability to remain malleable at extremely low temperatures and its soft, pliable nature that fills imperfections in mating metal surfaces, creating a hermetic seal. Unlike many materials used for sealing at standard operating temperatures, which may crack and break at cryogenic temperatures, Indium Wire maintains its integrity.
In cryogenic or other sealing applications where seals must be made within channels or irregular features, Indium Wire’s ability to wet to glass, metal, and ceramic surfaces ensures effective sealing. It is available in a variety of diameters and custom shapes, including round, and can be supplied in custom continuous lengths to suit specific requirements.
Traditionally used for demountable cryogenic seals, Indium Wire’s ductility allows it to deform plastically to create a seal between flanges without embrittling upon cooling. It is also essential for ITO coatings in LCD displays, bonding glass and ceramics to metals, and creating high-vacuum seals in laboratory settings.
Notably, Indium Wire is non-toxic but should be handled with care to avoid skin contact or inhalation. It serves as a premium lead-free solder component, optimized for use with Sn/Pb and Pb-free assembly and rework processes. It offers excellent cleanability with cold water, fast wetting to common Pb-free surface finishes, minimal spattering, and low odor.
The 99.99% indium content in Indium Wire minimizes impurities, ensuring good weldability and oxidation resistance. This makes it an ideal choice for both wave soldering and dip soldering processes.
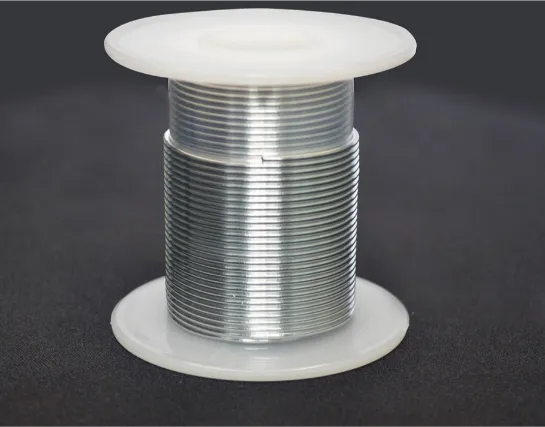