What Are Indium Interface Materials?
Indium interface materials are specialized solutions used in thermal management applications to enhance heat transfer and ensure optimal performance in electronic and industrial systems. These materials play a crucial role in creating reliable, efficient, and durable seals between two surfaces, particularly in environments requiring hermetic sealing or cryogenic compatibility.
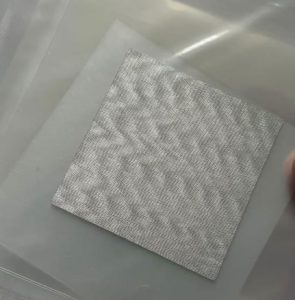
Understanding Thermal Interfaces
A thermal interface is the connection point between two objects through which thermal energy flows. Examples include the junction between a heat sink and a thermoelectric module (TEC). Achieving maximum thermal conductivity at these interfaces is essential for efficient heat dissipation, and indium provides an ideal solution for many applications.
The Science Behind Indium’s Effectiveness
Even when two surfaces appear flat and smooth, they are filled with microscopic peaks and valleys, reducing their actual contact area to approximately 5%. Indium’s unique properties, such as its malleability and thermal conductivity, allow it to fill these gaps effectively, creating a near-perfect thermal interface and significantly improving heat transfer.
Why Choose Indium for Thermal Management?
Indium stands out among thermal interface materials for its exceptional qualities. Its ability to form a chemical bond with surfaces under compression, even at cryogenic temperatures, makes it a reliable choice for critical applications. Additionally, indium’s resistance to oxidation, vibration, and mechanical shock ensures long-term stability.
Key Applications of Indium Interface Materials
Indium is used across a wide range of industries, including electronics, aerospace, cryogenics, and medical devices. Common applications include:
- Sealing in vacuum pumps and cryogenic systems.
- Heat-sensitive areas in electronic modules.
- Interfaces for glass, ceramic, and metallic components.
Types of Indium Interface Materials
Indium can be used in various forms to meet specific application requirements. These include:
- Indium Sheets and Foils: Ideal for creating flat seals with customizable thickness.
- Pre-Tinned Indium: Coated with a layer of indium or silver for enhanced bonding.
- Indium O-Rings and Gaskets: Engineered for precise sealing applications.
Preparation of Surfaces for Indium Seals
Proper surface preparation is vital for ensuring the effectiveness of indium seals. The process involves:
- Cleaning: Remove oils and debris using degreasing solvents or ultrasonic cleaning.
- Polishing: Achieve a fine finish using abrasive powders or machining.
- Etching: For critical applications, oxide layers on indium can be removed with a 50% hydrochloric acid dip.
Advantages of Indium Interface Materials
Indium offers numerous benefits over conventional thermal interface materials, such as:
- High thermal conductivity.
- Excellent mechanical compliance under pressure.
- Compatibility with cryogenic and high-temperature environments.
- Long-term durability with minimal performance degradation.
Factors Affecting the Quality of Indium Seals
The performance of indium seals depends on several factors, including:
- Čistota: A minimum purity of 99.99% is recommended for most applications.
- Seal Design: Proper sizing and compression ensure effective sealing.
- Application Environment: Consideration of temperature and mechanical stresses.
Indium vs. Other Thermal Interface Materials
Indium surpasses traditional TIMs, such as thermal greases and pads, in many aspects. Unlike greases that may degrade over time, indium provides a stable, reusable solution with superior thermal and mechanical properties.
Conclusion: The Future of Indium in Thermal Interfaces
Indium interface materials are revolutionizing the field of thermal management with their unmatched combination of thermal conductivity, flexibility, and reliability. By optimizing heat transfer and ensuring durable seals, indium is paving the way for advancements in electronic cooling, cryogenics, and beyond.