Pengedap Vakum Indium menonjol sebagai bahan unggul untuk mencipta pengedap hermetik yang ketat helium, merapatkan logam dan substrat bukan logam seperti kaca dan seramik. Fleksibilitinya meluas ke persekitaran kriogenik, pam vakum, dan kawasan sensitif haba, di mana ia memastikan pembendungan yang boleh dipercayai.
Apabila indium berfungsi sebagai pengedap, ia memulakan ikatan kimia dengan permukaan yang disambungkannya, berbeza daripada pembentukan penghalang semata-mata bahan gasket lain. Terutamanya, pengedap indium menunjukkan daya tahan terhadap kejutan mekanikal, getaran dan suhu yang melampau, menjadikannya sangat diperlukan dalam aplikasi yang menuntut.
Sifat indium yang wujud ialah kecenderungannya untuk menghasilkan filem oksida pada permukaannya. Untuk mewujudkan ikatan murni dengan substrat, filem ini mesti terganggu melalui mampatan dan ubah bentuk plastik. Proses ini, difasilitasi oleh kebolehtempaan indium, berlaku dengan mudah walaupun pada suhu kriogenik, memastikan pengedap yang berkesan.
Kualiti sebuah meterai indium bergantung kepada beberapa faktor:
- Kesucian dan kebersihan: Tahap ketulenan Indium optimum 99.99% diutamakan, walaupun aplikasi terpilih menuntut ketulenan Indium 99.999%. Bahan cemar, terutamanya sebatian organik, harus disingkirkan melalui penyahgris. Oksida permukaan boleh disingkirkan dengan celupan singkat dalam asid hidroklorik 50%, diikuti dengan pembilasan dalam air ternyahion.
- Persediaan permukaan: Semua permukaan mesti menjalani pembersihan dan pengeringan yang menyeluruh. Permukaan kaca dan seramik memerlukan rawatan dengan asid kromik dan sulfurik, diikuti dengan asid hidroklorik dan bilas air ternyahion. Permukaan logam Indium mungkin terdedah, pra-tindih dengan indium, atau disalut dengan indium atau perak. Kemasan permukaan hendaklah dilaksanakan dengan berhati-hati, tanpa menggilap berlebihan atau perubahan yang melelas.
- Ketebalan dan bentuk indium: Ketebalan Indium Seal berbeza-beza berdasarkan luas permukaan dan daya mampatan. Aplikasi alur cincin Indium 'O', meterai Indium harus melebihi dimensi alur sebanyak 5-15% apabila dimampatkan. Segmen indium yang bertindih boleh menggantikan mesin basuh berterusan dalam senario tertentu. Pengedap yang terbentuk dengan baik menunjukkan kadar kebocoran di bawah 2 x 10-7 torr x liter/saat.
Dengan mematuhi prosedur yang teliti untuk pemilihan indium, penyediaan permukaan, dan konfigurasi meterai, jurutera boleh memastikan kebolehpercayaan dan keberkesanan pengedap hermetik dalam aplikasi kritikal.
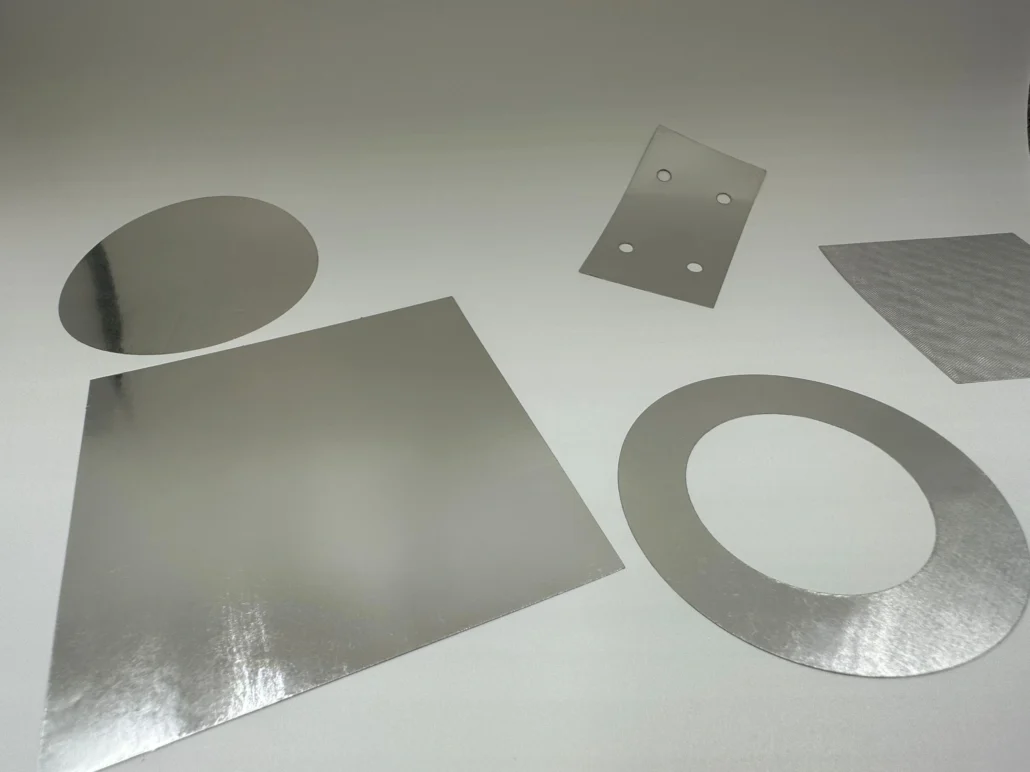
Ciri-ciri fizikal
Salah satu sifat fizikal yang paling ketara bagi indium adalah kemuluran dan kebolehtempaan yang luar biasa. Indium mempunyai kekerasan Mohs hanya 1.2, jauh lebih rendah daripada kuprum (2.5-3) dan aluminium (2-2.9), menjadikannya lebih lembut dan mudah berubah bentuk.
Ia mempunyai takat lebur yang agak rendah iaitu 156.6°C, membolehkan ia mudah dibentuk ke dalam pelbagai bentuk dan saiz, seperti prabentuk dan wayar, agar sesuai dengan aplikasi pengedap tertentu.
Indium boleh dibuat mengikut ketebalan antara nipis (0.008 inci) hingga tebal (0.062 inci), bergantung pada permukaan mengawan dan daya mampatan yang diperlukan.
Sifat Kimia
Ciri-ciri Pengedap
IndiumKeupayaan untuk membentuk pengedap hermetik tanpa memerlukan haba amat berfaedah dalam persekitaran yang haba atau fluks pateri mungkin menyebabkan isu seperti keluar gas.
Apabila digunakan sebagai pengedap, indium memulakan ikatan kimia dengan permukaan yang disambungkannya, menawarkan keupayaan pengedap yang unggul berbanding bahan gasket lain yang hanya bertindak sebagai penghalang.
Sifat ini membolehkan pengedap indium mengekalkan integritinya walaupun di bawah kejutan mekanikal, getaran dan suhu yang melampau, menjadikannya sangat diperlukan dalam aplikasi yang menuntut.
Persediaan permukaan
Penyediaan permukaan yang betul adalah penting untuk mencapai pengedap indium berkualiti tinggi. Permukaan mesti dibersihkan dan dikeringkan dengan teliti, dengan rawatan khusus untuk bahan yang berbeza. Sebagai contoh, permukaan kaca dan seramik hendaklah dirawat dengan asid kromik dan sulfurik, diikuti dengan asid hidroklorik dan bilas air ternyahion.
Logam indium permukaan mungkin memerlukan pra-tinning atau penyaduran dengan indium atau perak untuk memastikan ikatan optimum.
Penyingkiran oksida permukaan melalui pemampatan dan ubah bentuk plastik dipermudahkan oleh kebolehtempaan indium, memastikan pengedap yang berkesan walaupun pada suhu kriogenik.
Fleksibiliti Indium meluas kepada penggunaannya dalam membentuk pengedap hermetik yang ketat helium, mampu merapatkan logam dan substrat bukan logam seperti kaca dan seramik. Ini menjadikan indium sebagai bahan penting dalam aplikasi yang memerlukan prestasi yang boleh dipercayai dalam pam vakum, persekitaran kriogenik dan kawasan sensitif haba yang lain.
Teknologi Pengedap Vakum Indium
Teknologi pengedap vakum Indium memanfaatkan sifat unik indium untuk mencipta pengedap yang boleh dipercayai dan berkesan dalam pelbagai aplikasi, termasuk persekitaran kriogenik, pam vakum dan kawasan sensitif haba.
Teknologi ini amat dihargai kerana keupayaannya membentuk pengedap hermetik yang ketat helium, merapatkan kedua-dua substrat logam dan bukan logam seperti kaca dan seramik.
Sifat dan Kelebihan
Indium dicirikan oleh takat leburnya yang rendah, kebolehtempaan yang tinggi, dan kemuluran, yang menjadikannya bahan yang sesuai untuk pengedap vakum.
Tidak seperti gasket yang diperbuat daripada bahan lain yang hanya membentuk penghalang, indium mencipta ikatan kimia dengan permukaan yang disambungkannya, meningkatkan daya tahan pengedap terhadap kejutan mekanikal, getaran dan suhu rendah.
Satu ciri yang ketara bagi indium ialah kecenderungannya untuk menghasilkan filem oksida pada permukaannya. Untuk mewujudkan ikatan murni dengan substrat, filem oksida ini mesti terganggu melalui mampatan dan ubah bentuk plastik, satu proses yang difasilitasi oleh kebolehtempaan logam.
Ini memastikan pengedap yang berkesan walaupun pada suhu kriogenik tanpa memerlukan haba.
Aplikasi
Pengedap vakum indium mempunyai pelbagai aplikasi kerana sifat uniknya dan keupayaan untuk beroperasi dengan berkesan dalam keadaan yang melampau. Kepelbagaian meterai indium menjadikannya sesuai untuk industri daripada aeroangkasa dan automotif kepada sektor perubatan dan perindustrian.
Aeroangkasa dan Automotif
Dalam sektor aeroangkasa dan automotif, pengedap indium digunakan untuk sifat pengedap yang sangat baik dan keupayaan mereka untuk mengekalkan vakum di bawah keadaan tekanan tinggi dan suhu tinggi. Ini memastikan integriti komponen dan sistem yang beroperasi dalam persekitaran yang keras.
Perubatan dan Perindustrian
Aplikasi perubatan dan industri pengedap vakum indium adalah meluas. Pengedap indium digunakan dalam peranti dan peralatan perubatan yang memerlukan ketulenan dan kebolehpercayaan yang tinggi, seperti alat diagnostik dan bioimplan. Sebagai contoh, diagnostik perubatan dan tempat penjagaan yang diperibadikan (POC) selalunya bergantung pada peranti yang beroperasi pada tahap molekul, di mana fungsi pengedap yang tepat adalah penting.
Integrasi Teknologi Pintar
Trend yang semakin meningkat dalam reka bentuk meterai indium ialah integrasi teknologi pintar. Dengan pengembangan Internet Perkara (IoT), terdapat peningkatan permintaan untuk penyelesaian pengedap yang boleh memantau dan mengawal pelbagai proses dalam masa nyata. Pengedap Indium sangat sesuai untuk aplikasi ini kerana sifat uniknya, membolehkan ia digunakan dalam pelbagai senario. Dengan menggabungkan penderia dan peranti pintar lain ke dalam pengedap indium, pengeluar boleh mencipta penyelesaian pengedap yang lebih cekap dan pintar.
Teknik Analisis Permukaan
Dalam bidang aplikasi vakum ultra-tinggi (UHV), pengedap indium adalah penting untuk mengekalkan keadaan vakum yang diperlukan untuk teknik analisis permukaan. Teknik ini termasuk spektroskopi fotoelektron sinar-X (XPS), spektroskopi elektron Auger (AES), spektrometri jisim ion sekunder (SIMS), dan lain-lain. Keadaan UHV adalah penting untuk mengurangkan pencemaran permukaan semasa analisis ini. Pengedap indium membantu mencapai keadaan vakum yang ketat yang diperlukan untuk teknik ketepatan tinggi ini, membolehkan pengukuran yang tepat dan boleh dipercayai.
Teknologi Baru Muncul
Teknologi baru muncul seperti sifat anti-kotoran, bioimplan, dan peranti diagnostik juga mendapat manfaat daripada penggunaan pengedap vakum indium. Aplikasi ini memerlukan pemahaman asas tentang antara muka bio dan keupayaan untuk mengekalkan persekitaran steril dan bebas bahan cemar. Pengedap Indium menyumbang dengan ketara kepada bidang ini dengan menyediakan penyelesaian pengedap yang boleh dipercayai yang memenuhi permintaan ketat teknologi moden.
Ringkasan
An meterai vakum indium ialah teknologi pengedap khusus yang memanfaatkan sifat unik indium, logam pasca peralihan yang terkenal dengan kebolehtempaan, kemuluran dan keupayaan untuk membentuk pengedap hermetik. Pengedap vakum indium sangat dihargai kerana keupayaannya membentuk pengedap hermetik kedap helium dengan mengikat secara kimia dengan permukaan yang disambungkan. Ikatan kimia ini, berbanding hanya bertindak sebagai penghalang, memastikan keupayaan pengedap yang unggul yang menahan kejutan mekanikal, getaran dan suhu yang melampau.