Sigillo sottovuoto in indio si distingue come materiale superiore per la creazione di guarnizioni ermetiche a tenuta di elio, per collegare metalli e substrati non metallici come vetro e ceramica. La sua versatilità si estende agli ambienti criogenici, alle pompe per vuoto e alle aree sensibili al calore, dove garantisce un contenimento affidabile.
Quando l'indio funge da sigillante, avvia un legame chimico con le superfici che collega, distinto dalla semplice formazione di barriera di altri materiali per guarnizioni. In particolare, le guarnizioni in indio dimostrano resistenza agli shock meccanici, alle vibrazioni e alle temperature estreme, rendendole indispensabili nelle applicazioni più impegnative.
Una proprietà intrinseca dell'indio è la sua tendenza a sviluppare una pellicola di ossido sulla sua superficie. Per stabilire un legame perfetto con un substrato, questo film deve essere distrutto attraverso la compressione e la deformazione plastica. Questo processo, facilitato dalla malleabilità dell'indio, avviene facilmente anche a temperature criogeniche, garantendo un'efficace sigillatura.
La qualità di un sigillo dell'indio dipende da diversi fattori:
- Purezza e pulizia: Sono preferibili livelli ottimali di purezza dell'indio di 99.99%, sebbene applicazioni selezionate richiedano la purezza dell'indio 99.999%. I contaminanti, soprattutto i composti organici, devono essere rimossi mediante sgrassaggio. Gli ossidi superficiali possono essere eliminati con una breve immersione in acido cloridrico 50%, seguita da un risciacquo in acqua deionizzata.
- Preparazione della superficie: Tutte le superfici devono essere sottoposte ad un'accurata pulizia ed asciugatura. Le superfici in vetro e ceramica richiedono un trattamento con acido cromico e solforico, seguiti da acido cloridrico e risciacquo con acqua deionizzata. Indio Le superfici metalliche possono essere nude, pre-stagnate con indio o placcate con indio o argento. La finitura superficiale deve essere eseguita con attenzione, senza lucidatura eccessiva o alterazioni abrasive.
- Spessore e forma dell'indio: Lo spessore della guarnizione indio varia in base alla superficie e alla forza di compressione. Nelle applicazioni con scanalatura dell'O-ring in indio, la guarnizione in indio dovrebbe superare le dimensioni della scanalatura di 5-15% quando compressa. Segmenti sovrapposti di indio possono sostituire una rondella continua in determinati scenari. Le guarnizioni ben formate mostrano tassi di perdita inferiori a 2 x 10-7 torr x litro/sec.
Aderendo a procedure meticolose per la selezione dell'indio, la preparazione della superficie e la configurazione delle guarnizioni, gli ingegneri possono garantire l'affidabilità e l'efficacia delle guarnizioni ermetiche nelle applicazioni critiche.
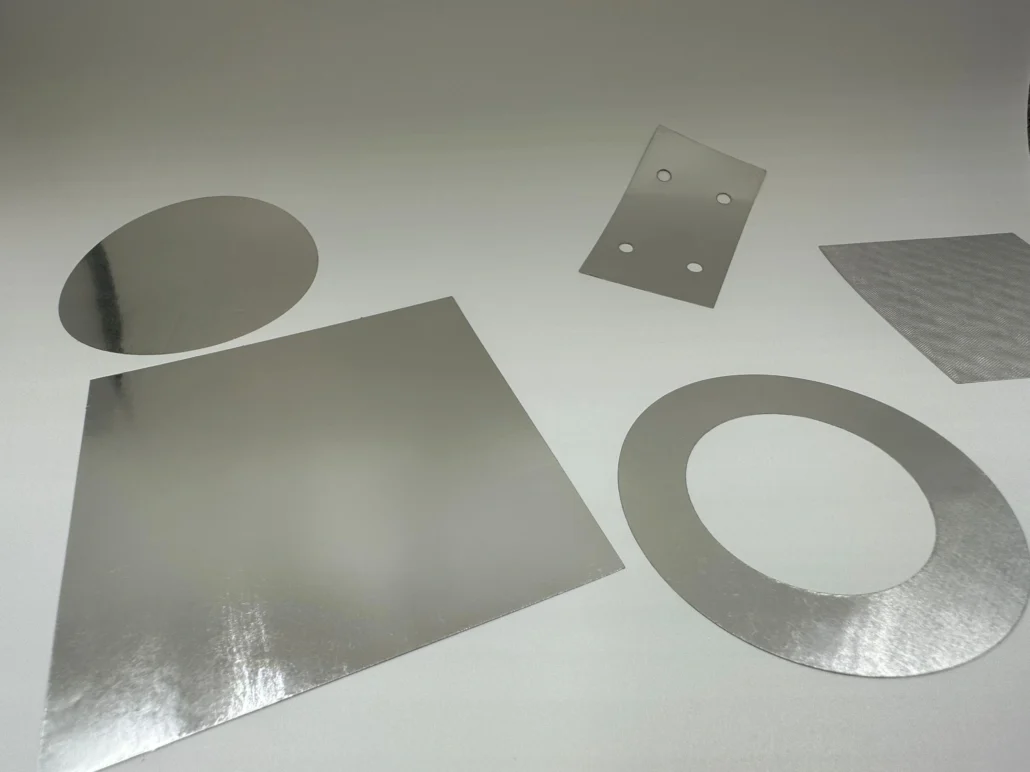
Proprietà fisiche
Una delle proprietà fisiche più notevoli di indio è la sua eccezionale duttilità e malleabilità. L'indio possiede una durezza Mohs di appena 1,2, significativamente inferiore a quella del rame (2,5-3) e dell'alluminio (2-2,9), il che lo rende molto più morbido e facile da deformare.
Ha un punto di fusione relativamente basso, pari a 156,6 °C, che gli consente di essere facilmente modellato in varie forme e dimensioni, come preforme e fili, per adattarsi ad applicazioni di tenuta specifiche.
L'indio può essere lavorato in spessori che vanno da sottili (0,008 pollici) a spessi (0,062 pollici), a seconda delle superfici di accoppiamento e delle forze di compressione richieste.
Proprietà chimiche
Caratteristiche di tenuta
IndioLa capacità di formare guarnizioni ermetiche senza bisogno di calore è particolarmente vantaggiosa in ambienti in cui il calore o il flusso di saldatura potrebbero causare problemi come il degassamento.
Quando viene utilizzato come sigillante, l'indio crea un legame chimico con le superfici che collega, offrendo capacità di tenuta superiori rispetto ad altri materiali per guarnizioni che agiscono semplicemente come barriere.
Questa proprietà consente alle guarnizioni in indio di mantenere la loro integrità anche in caso di urti meccanici, vibrazioni e temperature estreme, rendendole indispensabili nelle applicazioni più impegnative.
Preparazione della superficie
Una corretta preparazione della superficie è fondamentale per ottenere guarnizioni in indio di alta qualità. Le superfici devono essere pulite e asciugate accuratamente, con trattamenti specifici per i diversi materiali. Ad esempio, le superfici in vetro e ceramica devono essere trattate con acido cromico e solforico, seguiti da un risciacquo con acido cloridrico e acqua deionizzata.
Indio metallico le superfici potrebbero richiedere una pre-stagnatura o una placcatura con indio o argento per garantire una saldatura ottimale.
La rimozione degli ossidi superficiali mediante compressione e deformazione plastica è facilitata dalla malleabilità dell'indio, garantendo una tenuta efficace anche a temperature criogeniche.
La versatilità dell'indio si estende al suo utilizzo nella formazione di guarnizioni ermetiche a tenuta di elio, in grado di collegare metalli e substrati non metallici come vetro e ceramica. Ciò rende l'indio un materiale essenziale nelle applicazioni che richiedono prestazioni affidabili in pompe per vuoto, ambienti criogenici e altre aree sensibili al calore.
Tecnologia di sigillatura sottovuoto all'indio
Tecnologia di sigillatura sottovuoto all'indio sfrutta le proprietà uniche dell'indio per creare guarnizioni affidabili ed efficaci in una vasta gamma di applicazioni, tra cui ambienti criogenici, pompe per vuoto e aree sensibili al calore.
Questa tecnologia è particolarmente apprezzata per la sua capacità di formare guarnizioni ermetiche a tenuta di elio, collegando sia substrati metallici che non metallici come vetro e ceramica.
Proprietà e vantaggi
Indio è caratterizzato dal basso punto di fusione, dall'elevata malleabilità e duttilità, che lo rendono un materiale ideale per la sigillatura sotto vuoto.
A differenza delle guarnizioni realizzate con altri materiali che formano solo una barriera, l'indio crea un legame chimico con le superfici che collega, migliorando la resistenza della guarnizione agli urti meccanici, alle vibrazioni e alle basse temperature.
Una caratteristica notevole dell'indio è la sua tendenza a sviluppare una pellicola di ossido sulla sua superficie. Per stabilire un legame incontaminato con un substrato, questa pellicola di ossido deve essere interrotta tramite compressione e deformazione plastica, un processo facilitato dalla malleabilità del metallo.
Ciò garantisce una tenuta efficace anche a temperature criogeniche, senza bisogno di calore.
Applicazioni
Guarnizioni sottovuoto in indio hanno una vasta gamma di applicazioni grazie alle loro proprietà uniche e alla capacità di funzionare efficacemente in condizioni estreme. La versatilità delle guarnizioni in indio le rende adatte a settori che spaziano dall'aerospaziale all'automotive, fino al settore medico e industriale.
Aerospaziale e automobilistico
Nei settori aerospaziale e automobilistico, le guarnizioni in indio sono utilizzate per le loro eccellenti proprietà di tenuta e la loro capacità di mantenere il vuoto in condizioni di alta pressione e alta temperatura. Ciò garantisce l'integrità di componenti e sistemi che operano in ambienti difficili.
Medico e industriale
Le applicazioni mediche e industriali delle guarnizioni sottovuoto in indio sono estese. Le guarnizioni in indio sono utilizzate in dispositivi e apparecchiature mediche che richiedono elevata purezza e affidabilità, come strumenti diagnostici e bioimpianti. Ad esempio, la medicina personalizzata e la diagnostica point of care (POC) spesso si basano su dispositivi che operano a livello molecolare, dove il funzionamento preciso delle guarnizioni è fondamentale.
Integrazione della tecnologia intelligente
Una tendenza crescente in design del sigillo indio è l'integrazione della tecnologia intelligente. Con l'espansione dell'Internet of Things (IoT), c'è una crescente domanda di soluzioni di tenuta in grado di monitorare e controllare vari processi in tempo reale. Le guarnizioni in indio sono adatte a queste applicazioni grazie alle loro proprietà uniche, che consentono loro di essere utilizzate in un'ampia gamma di scenari. Incorporando sensori e altri dispositivi intelligenti nelle guarnizioni in indio, i produttori possono creare soluzioni di tenuta più efficienti e intelligenti.
Tecniche di analisi di superficie
Nel campo delle applicazioni di ultra-alto vuoto (UHV), le guarnizioni in indio sono fondamentali per mantenere le condizioni di vuoto necessarie per le tecniche di analisi di superficie. Queste tecniche includono la spettroscopia fotoelettronica a raggi X (XPS), la spettroscopia elettronica Auger (AES), la spettrometria di massa a ioni secondari (SIMS) e altre. Le condizioni UHV sono essenziali per ridurre la contaminazione superficiale durante queste analisi. Le guarnizioni in indio aiutano a raggiungere le rigorose condizioni di vuoto richieste per queste tecniche ad alta precisione, consentendo misurazioni accurate e affidabili.
Tecnologie emergenti
Anche le tecnologie emergenti come le proprietà anti-fouling, i bioimpianti e i dispositivi diagnostici traggono vantaggio dall'uso di guarnizioni sottovuoto in indio. Queste applicazioni richiedono una comprensione fondamentale delle biointerfacce e la capacità di mantenere ambienti sterili e privi di contaminanti. Le guarnizioni in indio contribuiscono in modo significativo a questi campi fornendo soluzioni di tenuta affidabili che soddisfano le rigorose richieste della tecnologia moderna.
Riepilogo
UN guarnizione sottovuoto in indio è una tecnologia di tenuta specializzata che sfrutta le proprietà uniche dell'indio, un metallo post-transizione noto per la sua malleabilità, duttilità e capacità di formare guarnizioni ermetiche. Le guarnizioni sottovuoto in indio sono molto apprezzate per la loro capacità di formare guarnizioni ermetiche a tenuta di elio legandosi chimicamente alle superfici che collegano. Questo legame chimico, anziché agire semplicemente come barriera, garantisce capacità di tenuta superiori che resistono a urti meccanici, vibrazioni e temperature estreme.