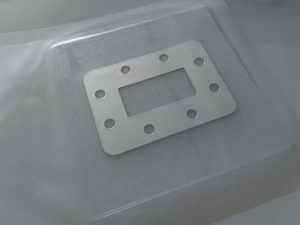
Lợi ích của hàn Indium
Hàn Indi mang lại nhiều lợi ích trong nhiều ứng dụng công nghiệp khác nhau, đặc biệt là trong lĩnh vực điện tử. Một trong những lợi thế chính của nó là vai trò trong quản lý nhiệt cho chip máy tính hiệu suất cao, trong đó độ dẫn nhiệt cao và điểm nóng chảy thấp làm cho nó trở thành một Vật liệu giao diện nhiệt (TIM). Điều này đảm bảo tản nhiệt hiệu quả, yếu tố rất quan trọng để duy trì hiệu suất và tuổi thọ tối ưu của thiết bị.
Trong lắp ráp điện tử, hàn indi đặc biệt được đánh giá cao vì tính linh hoạt của nó. Nó được sử dụng rộng rãi để niêm phong các thiết bị hồng ngoại do khả năng niêm phong đặc biệt của nó, đảm bảo tính ổn định của thiết bị và độ tin cậy lâu dài. Ngoài ra, ứng dụng của nó như một TIM trong các thiết bị công suất cao giúp tăng cường tản nhiệt, kéo dài tuổi thọ hoạt động của các thiết bị này.
Điểm nóng chảy thấp của chất hàn indium là một lợi ích đáng kể khác, đặc biệt là trong sản xuất các linh kiện điện tử nhạy cảm với nhiệt độ. Việc sử dụng nó làm giảm nguy cơ làm hỏng các linh kiện nhạy cảm trong quá trình hàn. Điều này đặc biệt có lợi trong các ứng dụng như hàn từng bước, khi cần nhiệt độ nóng chảy thấp hơn để gắn các linh kiện mỏng manh sau khi các quy trình hàn tiêu chuẩn đã hoàn tất. Điểm nóng chảy thấp cũng giúp ngăn ngừa cong vênh của các chip mỏng hơn và rất quan trọng đối với mạch flex Tg thấp được sử dụng trong các thiết bị như điện thoại di động, đồng hồ thông minh và thiết bị IoT.
Việc tuân thủ các tiêu chuẩn môi trường hiện đại của chất hàn Indium cũng đáng chú ý. Là một giải pháp thay thế không chì, nó phù hợp với các quy định như chỉ thị Hạn chế các chất độc hại (RoHS), góp phần vào các hoạt động sản xuất bền vững hơn. Việc tuân thủ này giúp giảm tác động môi trường liên quan đến chất thải điện tử. Hơn nữa, chất hàn Indium có thể là một phần của đánh giá vòng đời rộng hơn, đánh giá các lợi ích về môi trường của nó so với các chất hàn chì truyền thống. Nó hỗ trợ các sản phẩm điện tử bền vững hơn bằng cách tạo điều kiện tái chế và giảm việc sử dụng vật liệu nguy hại.
Khả năng làm ướt tuyệt vời của chất hàn indium ảnh hưởng đến độ tin cậy và hiệu suất của các kết nối điện tử, đặc biệt là trong các thiết bị phức tạp. Tính chất này đảm bảo kết nối bền chắc với cả kim loại và phi kim loại, tạo ra điện trở thấp và độ dẻo cao. Nó đặc biệt có lợi trong các ứng dụng đòi hỏi độ tin cậy cao, chẳng hạn như đóng gói thiết bị chân không điện tử, thủy tinh, gốm sứ và thiết bị siêu dẫn nhiệt độ thấp.
Khả năng làm ướt vượt trội
Hàn Indium thể hiện khả năng làm ướt vượt trội, ảnh hưởng đáng kể đến độ tin cậy và hiệu suất của các kết nối điện tử trong các thiết bị phức tạp. Đặc tính này cho phép hàn lan rộng và bám dính hiệu quả vào nhiều bề mặt khác nhau, đảm bảo kết nối chắc chắn và nhất quán. Đặc biệt, chất hàn gốc indi thể hiện khả năng làm ướt tuyệt vời với cả kim loại và phi kim loại, điều này rất quan trọng để tạo thành mối hàn đáng tin cậy trong nhiều loại vật liệu được sử dụng trong thiết bị điện tử hiện đại. Ngoài ra, đặc tính làm ướt vượt trội này góp phần tạo ra điện trở thấp và độ dẻo cao của mối hàn, tăng cường độ bền và chức năng tổng thể của các linh kiện điện tử. Những đặc tính này làm cho chất hàn indium trở thành lựa chọn lý tưởng cho các ứng dụng đòi hỏi kết nối bền và đáng tin cậy, đặc biệt là trong các mạch điện thu nhỏ và dày đặc trong các thiết bị điện tử hiện đại.
Điểm nóng chảy thấp
Một trong những lợi thế chính của chất hàn indium là điểm nóng chảy thấp, mang lại lợi ích đáng kể trong quy trình sản xuất thiết bị điện tử. Chất hàn indium thường nóng chảy ở nhiệt độ dưới 180°C, khiến nó trở thành lựa chọn lý tưởng cho các ứng dụng liên quan đến các thành phần nhạy cảm với nhiệt độ. Điểm nóng chảy thấp này đặc biệt có lợi trong một số lĩnh vực chính.
Đầu tiên, nó cho phép gắn các thành phần nhạy cảm với nhiệt độ vào bảng mạch in mà không gây ra hư hỏng do nhiệt. Các vật liệu hàn truyền thống có điểm nóng chảy cao hơn có thể dẫn đến cong vênh các chip mỏng hơn và các thành phần khác do nhiệt độ cao cần thiết để hàn chảy lại. Ngược lại, điểm nóng chảy thấp của hàn indium làm giảm rủi ro này, đảm bảo tính toàn vẹn của các thành phần.
Ngoài ra, việc sử dụng chất hàn indium có điểm nóng chảy thấp là rất quan trọng trong các quy trình hàn từng bước. Điều này bao gồm việc gắn các thành phần trong một loạt các bước, trong đó mỗi bước sử dụng nhiệt độ nóng chảy thấp dần. Các thành phần tiêu chuẩn được hàn trước, sau đó là các thành phần nhạy cảm với nhiệt độ, được nóng chảy ở nhiệt độ dưới 180°C. Phương pháp này giúp bảo vệ chức năng của các thành phần mỏng manh, chẳng hạn như đèn LED, có thể bị hỏng do nhiệt độ cao hơn.
Hơn nữa, hàn indium là giải pháp có giá trị cho các ứng dụng liên quan đến các thiết bị mảng diện tích lớn, chẳng hạn như BGA (Mảng lưới bi). Nhiệt độ nóng chảy thấp hơn giúp tránh các vấn đề phổ biến như lỗi đầu vào gối (HIP) và lỗi không mở ướt (NWO), thường gặp khi sử dụng nhiệt độ cao hơn.
Cuối cùng, bản chất thân thiện với môi trường của chất hàn indium, đặc biệt là trong các hợp kim như Tin-Bismuth-Indium, khiến nó trở thành một sự thay thế hấp dẫn cho chất hàn chì truyền thống. Những chất hàn không chì này phù hợp với các tiêu chuẩn môi trường toàn cầu trong khi vẫn cung cấp hiệu suất tương tự, nếu không muốn nói là được cải thiện, trong các ứng dụng nhạy cảm với nhiệt độ và có độ tin cậy cao.
Dẫn nhiệt
Dây hàn indi đóng vai trò quan trọng trong việc quản lý nhiệt cho các chip điện toán hiệu suất cao. Khi hiệu suất chip và nhu cầu ứng dụng tiếp tục tăng, thiết kế nhiệt trở nên tối quan trọng, với indium được sử dụng rộng rãi làm Vật liệu giao diện nhiệt (TIM) do độ dẫn nhiệt cao, điểm nóng chảy thấp, dễ gia công và thân thiện với môi trường. Các loại thiết bị điện tử cụ thể được hưởng lợi đáng kể từ độ dẫn nhiệt của hàn indium bao gồm các thiết bị điện tử công suất cao, trong đó quản lý nhiệt hiệu quả là điều cần thiết. Hàn indium đóng vai trò là vật liệu giao diện nhiệt, tạo điều kiện tản nhiệt vượt trội, giúp tăng hiệu quả thiết bị và kéo dài tuổi thọ hoạt động, đảm bảo hiệu suất tối ưu trong những điều kiện đầy thách thức.
Lợi thế về môi trường và an toàn
Tuân thủ các quy định về môi trường
Hàn indium tuân thủ một số quy định nghiêm ngặt về môi trường góp phần đáng kể vào các hoạt động sản xuất bền vững trong ngành công nghiệp điện tử. Một trong những tiêu chuẩn chính là chỉ thị Hạn chế các chất độc hại (RoHS) của Liên minh châu Âu, chỉ thị này yêu cầu loại bỏ các hóa chất độc hại, bao gồm chì, khỏi các linh kiện điện tử. Luật này, có hiệu lực từ ngày 1 tháng 7 năm 2006, đã buộc các nhà sản xuất phải áp dụng các giải pháp thay thế không chứa chì, do đó giảm ô nhiễm môi trường và các rủi ro sức khỏe tiềm ẩn liên quan đến việc tiếp xúc với chì.
Hơn nữa, bản chất không chì của chất hàn indium phù hợp với sự chú trọng ngày càng tăng trên toàn cầu vào các hoạt động thân thiện với môi trường. Ví dụ, chất hàn Tin-Bismuth-Indium được công nhận vì các đặc tính thân thiện với môi trường, cung cấp một giải pháp thay thế khả thi và bền vững cho các chất hàn gốc chì truyền thống, đặc biệt là trong các ứng dụng nhạy cảm với nhiệt độ và có độ tin cậy cao. Sự thay đổi này không chỉ hỗ trợ đáp ứng các yêu cầu về quy định mà còn hỗ trợ ngành công nghiệp chuyển sang các quy trình sản xuất xanh hơn.
Ngoài ra, hàn indium giúp tiết kiệm năng lượng trong quá trình sản xuất. Việc sử dụng hàn nhiệt độ thấp, nóng chảy ở nhiệt độ dưới 180°C, có thể giảm đáng kể mức tiêu thụ năng lượng của lò nung nóng chảy trong lắp ráp điện tử. Việc giảm mức sử dụng năng lượng này không chỉ làm giảm chi phí vận hành mà còn giảm thiểu tác động đến môi trường của các hoạt động sản xuất.
Tác động đến Phân tích vòng đời của Sản phẩm điện tử
Việc sử dụng chất hàn indium làm chất thay thế không chì có ý nghĩa đáng kể đối với việc phân tích vòng đời của các sản phẩm điện tử về mặt tính bền vững của môi trường. Chương trình Thiết kế vì Môi trường (DfE) của EPA đã tiến hành đánh giá toàn diện vòng đời (LCA) để đánh giá tác động môi trường của nhiều loại chất hàn khác nhau, bao gồm cả các chất hàn thay thế không chì. Nghiên cứu đánh giá tác động của các loại chất hàn khác nhau đối với việc tái chế, thu hồi và khả năng thẩm thấu vào cuối vòng đời sản phẩm, đồng thời nhấn mạnh tầm quan trọng của việc lựa chọn vật liệu thân thiện với môi trường.
Đặc biệt, chất hàn indium mang lại một số lợi ích về môi trường. Một lợi thế đáng kể là điểm nóng chảy thấp, giúp giảm năng lượng cần thiết trong quá trình lắp ráp các sản phẩm điện tử. Việc giảm mức tiêu thụ năng lượng này chuyển thành lượng khí thải nhà kính thấp hơn, đóng góp tích cực vào tính bền vững của môi trường. Ngoài ra, chất hàn indium có thể thay thế các vật liệu nguy hiểm hơn, chẳng hạn như thủy ngân trong pin và có thể được sử dụng trong các tế bào quang điện và tấm pin mặt trời, thúc đẩy hơn nữa việc sử dụng các nguồn năng lượng tái tạo và giảm sự phụ thuộc vào nhiên liệu hóa thạch.
Hơn nữa, vai trò của indium trong quản lý giao diện nhiệt cho các thiết bị cao cấp giúp giảm nhiệt độ hoạt động tới 10°C, nâng cao hiệu quả năng lượng và tuổi thọ của các sản phẩm điện tử. Các khía cạnh này cùng nhau chỉ ra rằng việc kết hợp hàn indium trong sản xuất điện tử không chỉ giảm thiểu tác động đến môi trường trong quá trình sản xuất mà còn trong suốt vòng đời của sản phẩm, phù hợp với các mục tiêu phát triển bền vững.
Các ứng dụng
Hàn Indium đóng vai trò quan trọng trong việc tạo ra các mối hàn kín, rất cần thiết cho các ứng dụng có độ tin cậy cao trong nhiều ngành công nghiệp khác nhau. Mối hàn kín liên quan đến việc tạo ra các mối hàn kín khí ngăn không cho khí, chất lỏng và chất rắn đi qua, do đó bảo vệ các hệ thống điện tử khỏi các yếu tố môi trường. Công nghệ này đặc biệt quan trọng trong việc đảm bảo các linh kiện điện tử nhạy cảm vẫn được cách ly khỏi các chất gây ô nhiễm trong khi vẫn cho phép các tín hiệu điện và nguồn điện đi qua giữa các vỏ bọc.
Việc sử dụng chất hàn indium đặc biệt quan trọng trong các ứng dụng có độ tin cậy cao như các lĩnh vực ô tô, công nghiệp, hải quân, quân sự và hàng không vũ trụ. Các lĩnh vực này thường yêu cầu các vỏ bọc kín khí để bảo vệ các thành phần hệ thống bên trong khỏi các mối đe dọa từ môi trường bên ngoài, nếu không có thể dẫn đến hư hỏng, hỏng sớm hoặc giảm công suất. Bao bì kín khí, đạt được thông qua việc sử dụng chất hàn indium, cung cấp một gói được bảo vệ khỏi môi trường, ngăn chặn sự trao đổi giữa môi trường bên trong và bên ngoài, do đó tăng tuổi thọ và độ tin cậy của các thành phần, thiết bị và cụm lắp ráp RF/vi sóng quan trọng.
Hơn nữa, các đầu nối kín, thường dựa vào chất hàn indium, cung cấp khả năng bịt kín đặc biệt. Chúng được thiết kế để kín khí, ngăn hơi ẩm, bụi và các chất gây ô nhiễm khác xâm nhập vào hệ thống. Điều này rất quan trọng trong các môi trường khắc nghiệt như giàn khoan dầu, ứng dụng quân sự và công nghệ hàng không vũ trụ, nơi duy trì tính toàn vẹn của các kết nối điện.